Best Practices in Asset Management.
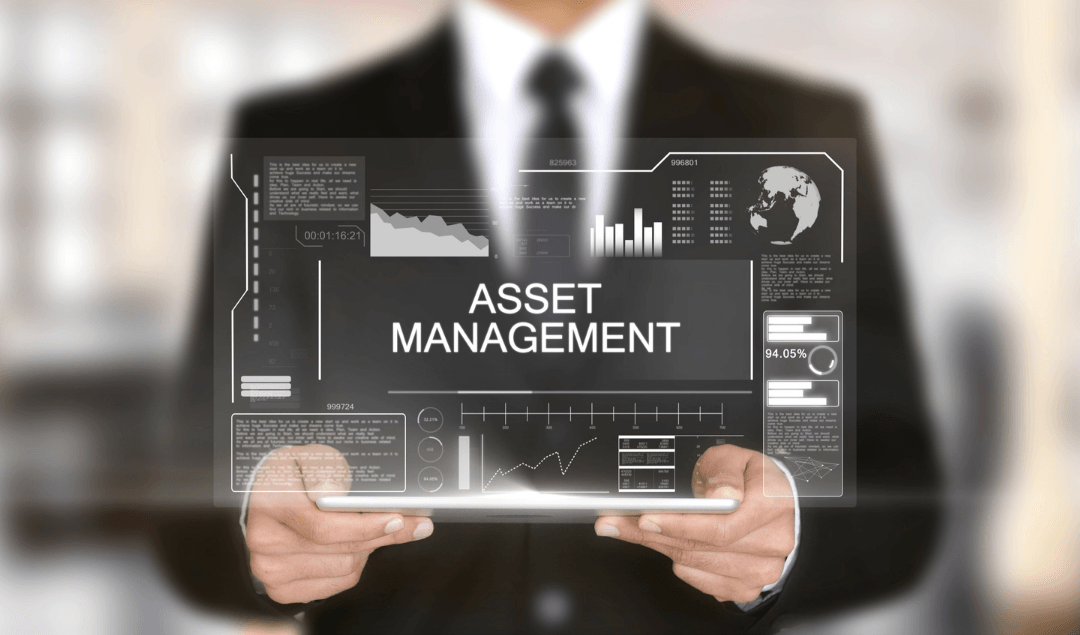
Managing assets efficiently has always been a significant challenge for any business as asset management is a necessity for maximizing business profits.
It is used as a cost-cutting measure to maintain and extend the life of equipment. Businesses rely on machine assets to manufacture the products they sell, as well as facility assets to support their manufacturing environments. When the cost of maintaining an asset outweighs the cost of replacing it, a new asset should be purchased as part of asset management. Successful asset management is made easier by implementing best practices and with the help of asset management software applications.
Asset management is an essential component of maintenance because it keeps assets running smoothly, resulting in efficient production. When assets are properly tracked and monitored, it ensures that equipment does not break down on a regular basis. Maintenance managers have a lot to consider and being able to effectively manage assets makes their job easier. Assets have a finite useful life. The asset's cost is spread out over its lifespan and, along with maintenance costs, accumulates as the asset depreciates. Proper asset maintenance, on the other hand, ensures that the asset's life is maximized while minimizing maintenance costs. Once an asset has been "paid off" by the revenue it generates, the revenue generated by the asset doing its job in production is applied to the organization's profits.
Asset management is also important because it increases the lifespan of expensive, critical assets. It makes the maintenance team's job easier in the long run because they can better predict when major repairs will be required, while emergency maintenance is reduced. Asset management entails more than just maintenance. While it is the maintenance team's responsibility to repair assets, perform preventive maintenance (PM), and design a system in which maintenance is better planned and predictable, some assets are designed to be run to failure without PM. Using assets that have already been paid off frees up funds for other capital improvements.
Asset Management Best Practices.
Asset Management Software Investment.
Investing in software or apps that support the most critical asset management requirements is one of the best asset management practices. A stellar software system will provide a central database for supplier information, warranties, site leases, and other important information. It will also include tools for optimizing maintenance workflow.
Automate and Improve Data Collection.
Automating and improving asset data collection is another asset management best practice. Integrating an asset management software system into facility, vehicle, and manufacturing asset management can improve data collection and access. The software's asset management features allow maintenance teams to quickly identify what equipment they have, where assets are located, and view service history to aid in troubleshooting.
In addition to manual methods, data is gathered by equipment sensors, which are installed to perform predictive maintenance (PdM). Internal wear that cannot be seen directly can be detected by these sensors. Machine learning and artificial intelligence can be used to perform advanced data analysis for predictive maintenance. The Internet of Things (IoT) is where data from PdM sensors is collected and stored in a database. Triggers in asset management solution software may be set to generate work orders based on specific asset conditions.
Keep Track of All Assets Owned.
An accurate inventory of all assets is useful for determining how many require maintenance and when. Knowing about all the assets that an organization uses ensures that maintenance can be tracked on each machine, vehicle, or facility. This information can be used to schedule maintenance with the least amount of disruption to production and to assign work orders based on which technicians are the most knowledgeable and experienced with each asset.
Uniquely Identify Assets.
It's also a good asset management practice to use a standard naming convention to uniquely identify all assets. There are nearly limitless possibilities for creating abbreviations for assets that make sense for a company. The key is to make them consistent and understandable to everyone in the organization who needs to use them.
Track Locations of Mobile Assets Using GPS Technology.
Keeping track of mobile assets is critical, particularly for organizations in industries with many vehicles. When a vehicle is on the job, GPS technology can pinpoint its exact location. This can be used to determine how long certain jobs take (including travel time) and where to send assistance more quickly if a vehicle breaks down.
Create Asset Tags.
Asset tags, when used on stationary assets, can pinpoint a machine's location within a facility. This ensures that maintenance technicians arrive at the correct asset at the correct time to perform maintenance. Asset tags can also be scanned, allowing information about the asset to be accessed via a mobile phone or tablet.
Make use of an Asset Hierarchy.
Using an asset hierarchy is another asset management best practice to implement. This enables maintenance teams to see how assets and their associated sub-components interact with one another. These connections aid in determining where most maintenance issues occur.
Have a Robust Failure Tracking Program.
Asset management should always include a robust failure tracking program. This includes asset history found in asset management software, the use of failure codes where appropriate, and the implementation of sensors to collect data for predictive maintenance (PdM) when possible.
Prioritize Safety.
When it comes to manufacturing asset management, another best practice is to prioritize safety. Asset maintenance necessitates attention to detail, which can mean the difference between a machine operating safely or not. A system should be put in place so that asset management procedures can be easily accessed. When necessary, modifications to these procedures should be made to improve safety.
Maintain Adequate Documentation.
Another best practice for asset management is to keep adequate asset documentation. User manuals and equipment schematics are the two main types of documentation that must be easily accessible and stored in the asset management software system. Maintenance personnel should locate paper documentation and scan or enter it into the software. They must search for digital files on various network drives or in email threads if necessary. They can also obtain documentation from the source, which is the vendor or manufacturer. Another option is to search the manufacturer's website, call a representative, or send an email to them.
Aside from asset documentation, maintenance teams should record repairs and preventive maintenance tasks in maintenance management software. Some data, such as asset history, is automatically updated based on how well the maintenance team uses their asset management software system. This can aid in deciding whether to repair or replace assets when they fail. When organizations purchase new asset management software or new assets, there may be a period of "catch up" time to ensure that all necessary data is entered into the system. This may appear to be a time-consuming process, but it is critical to collect and import as much data as possible because it will be useful for asset management in the future.
Set Quality and Usage Guidelines.
Setting asset usage guidelines for production staff is also part of the asset management process. When these guidelines are followed, maintenance personnel can streamline the maintenance schedule. When assets are operated correctly, there is less downtime due to machine misuse. Proper asset utilization also entails being aware of when assets must be available for maintenance. It is critical to maintain open communication between the maintenance and production departments prior to performing repairs or preventive maintenance tasks to avoid misunderstandings and scheduling conflicts.
Follow Warranty Guidelines.
Following warranty guidelines is critical from the day an asset is purchased and throughout its early lifecycle. Maintenance must be consistent in their asset inspections. It's also critical to follow all the manufacturer's maintenance recommendations. Equipment manufacturers provide recommendations for recommended maintenance schedules that outline which service tasks must be completed, the intervals at which maintenance must be performed, and what replacement parts will be required. Failure to do any or all these things may result in the manufacturer's warranty being voided. For example, if the maintenance team fails to perform regular furnace inspections and replace the filter, the manufacturer will refuse to replace a failed part or the entire furnace. Other things that will void a warranty include modifying a machine, changing a component without the authorization of an authorized technician, and modifying control software on equipment without the authorization of a certified technician.
Identify Critical Spares for Each Asset.
Identifying and stocking critical spares for each asset should be a best practice for any asset management organization. This can be accomplished using a bill of materials or by recording it elsewhere in the asset management software system. Asset management software solutions can also ensure that critical spares are available in inventory by tracking the quantities of each part in stock. If regular inspections are performed, having spare parts on hand ensures that they can be replaced as needed. Otherwise, the machine could be out of commission while maintenance awaits a delivery. These parts are kept in the inventory of Maintenance, Repair, and Operations (MRO), which also includes supplies and tools for completing maintenance work.
How Software Apps Support Asset Management.
There are many ways that asset management software can provide support for successful asset management. Here are some further benefits associated with having a solid software investment made.
· Provides a Centralized Database
· Visualizes Asset Relationships
· Keeps Detailed Maintenance Records
· Offers Asset Tags
· Provides a Robust Failure Tracking System
· Creates Bills of Materials and Identifying Critical Spares
· Uniquely Identifies Assets
· Improves Asset Performance through Reporting
· Schedules Recurring Maintenance
Improve your asset management challenges with MWare Automated Business Solutions.
We offer modern asset management capabilities to support the best practices you need to carry out machine maintenance.
To learn more about how MWare Automated Business Solutions offers a complete asset management software solution select one on the three options below.
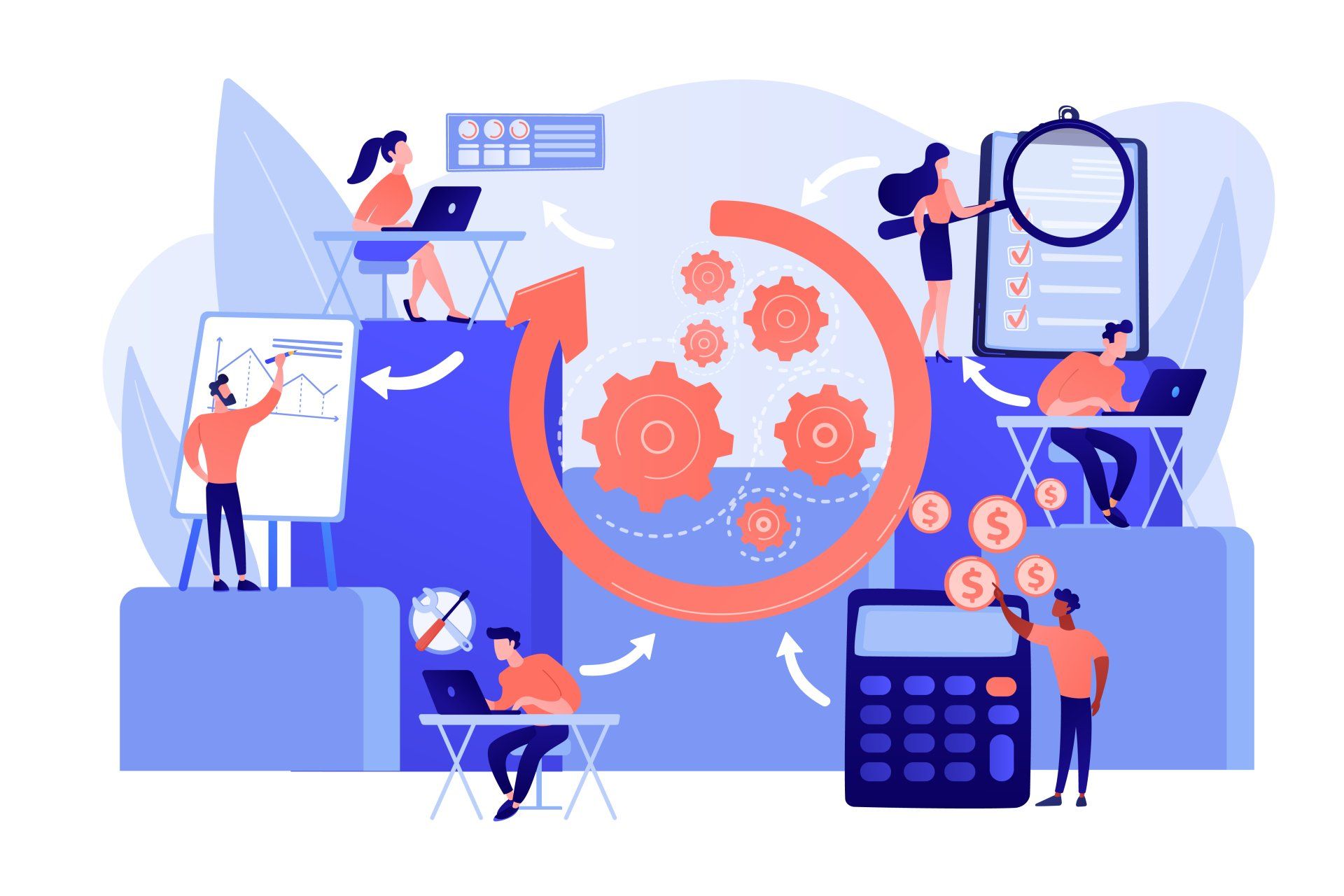
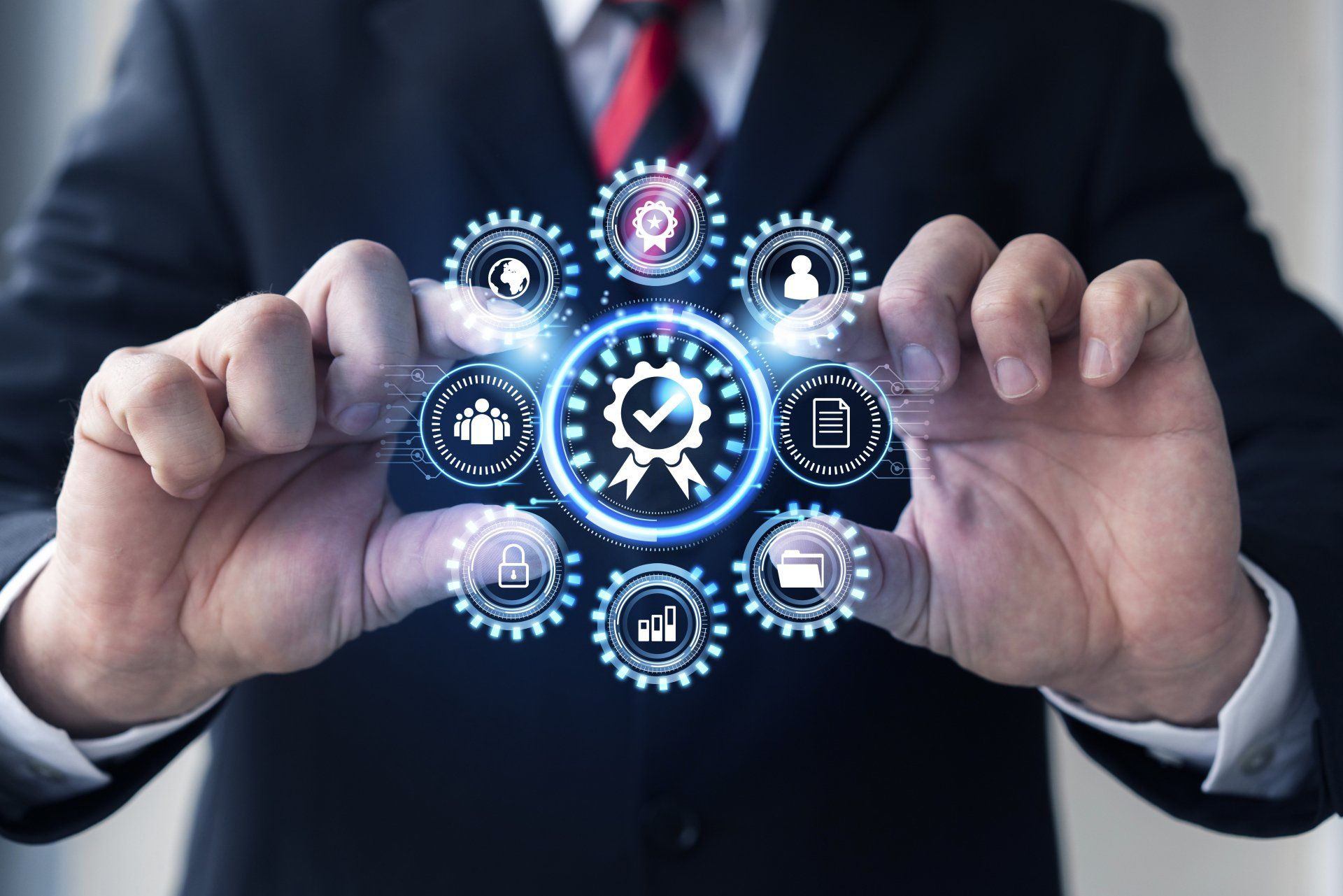
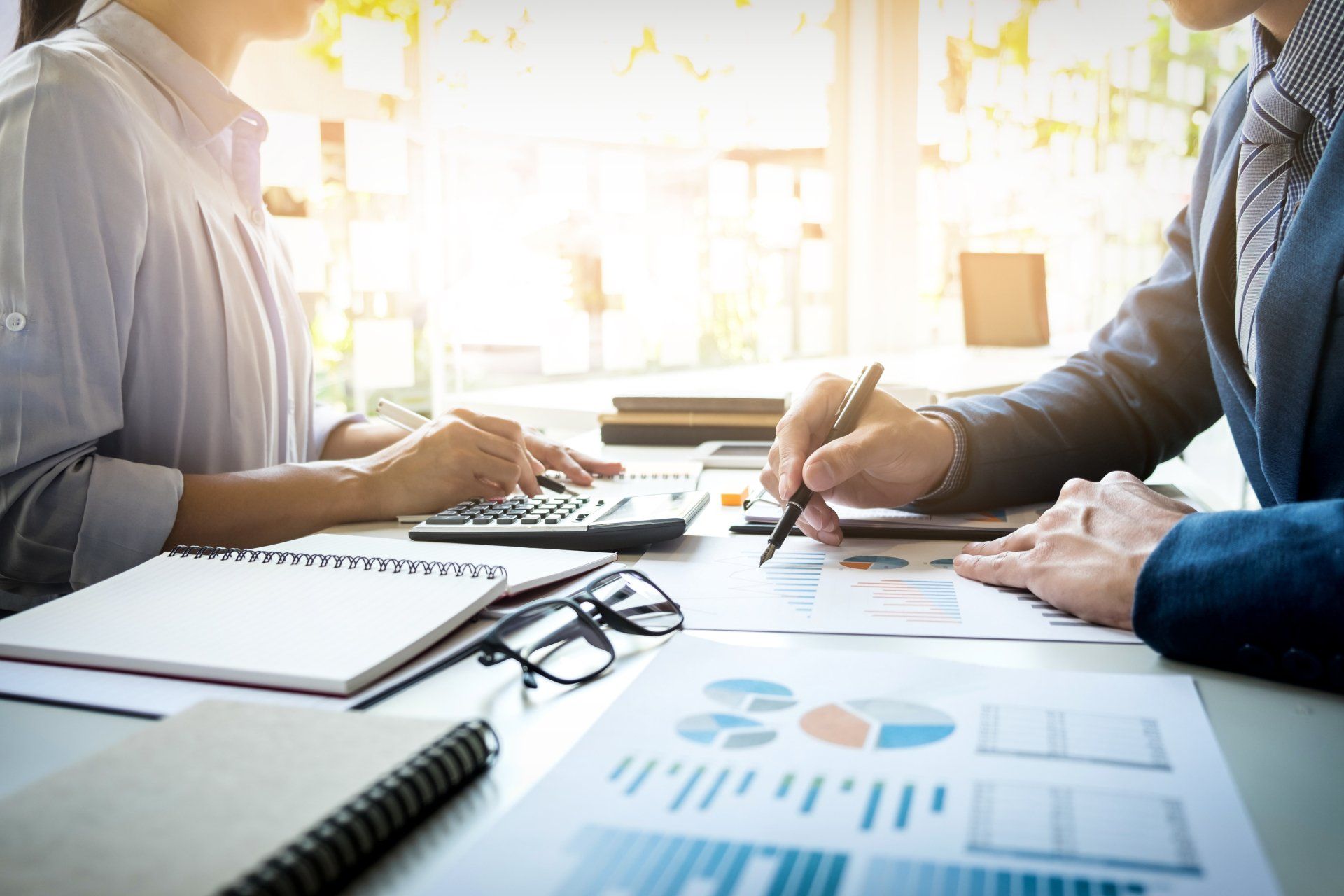
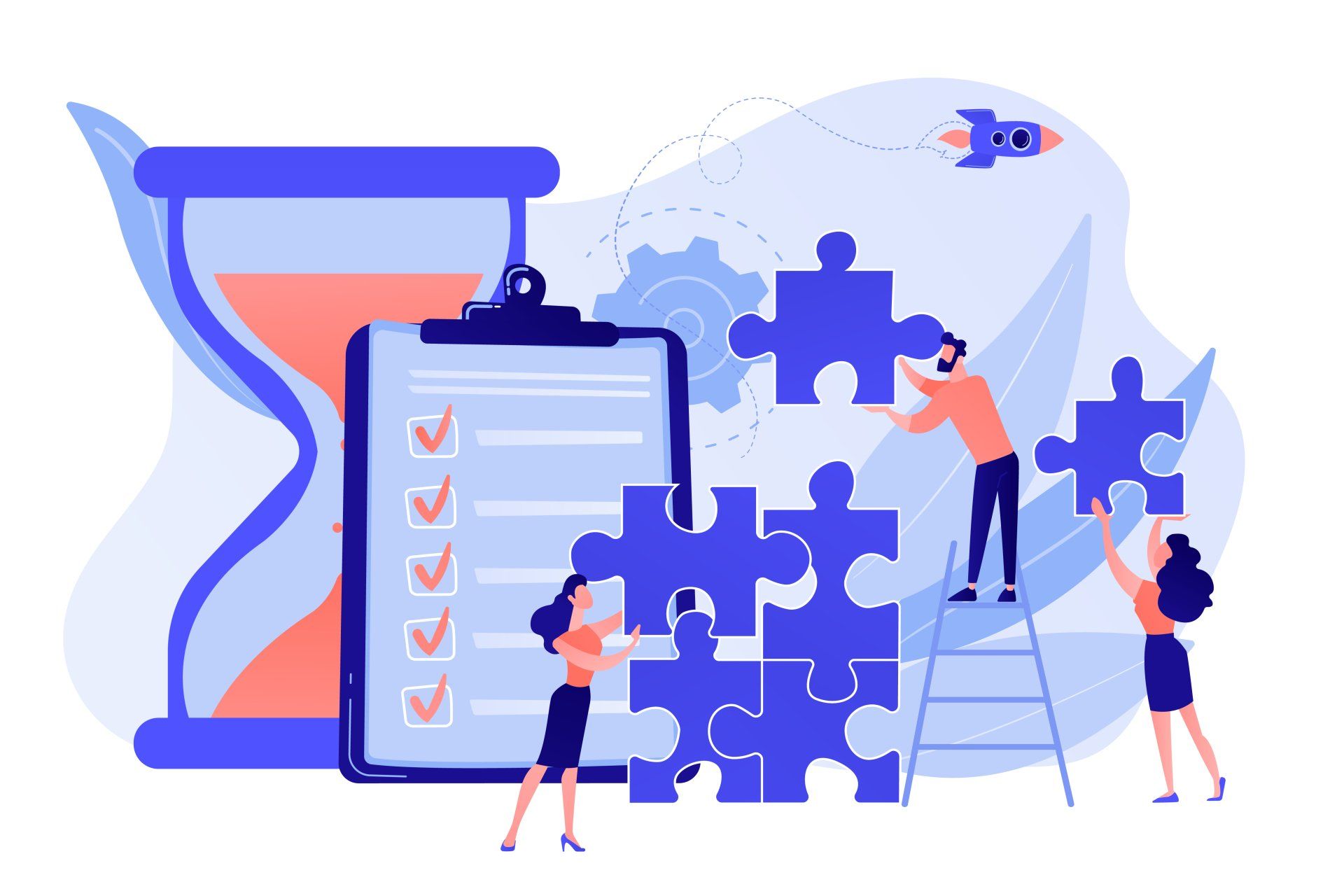
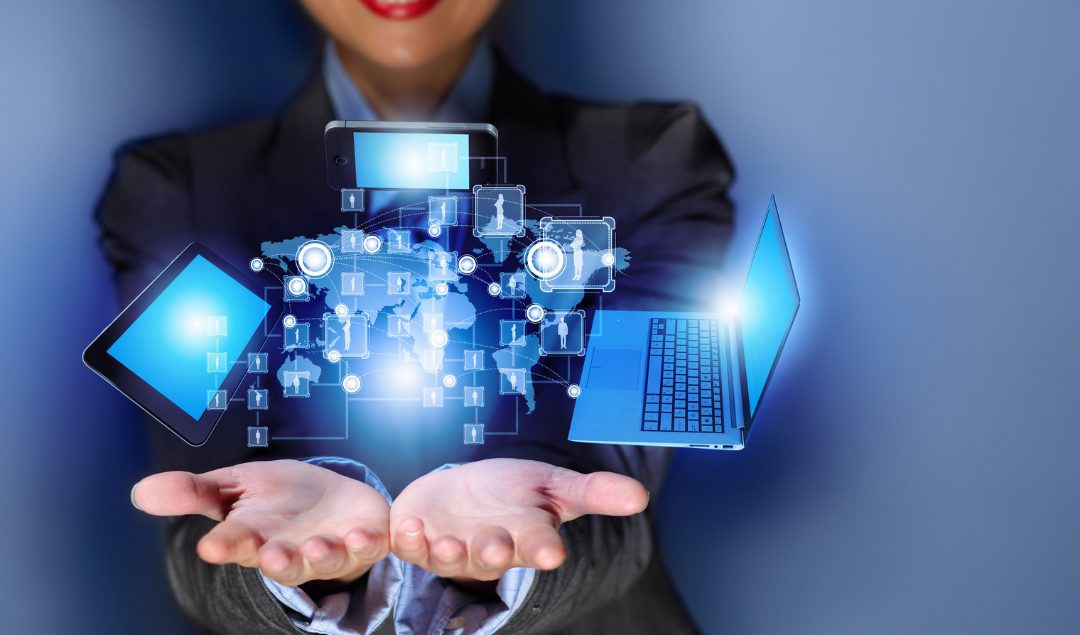
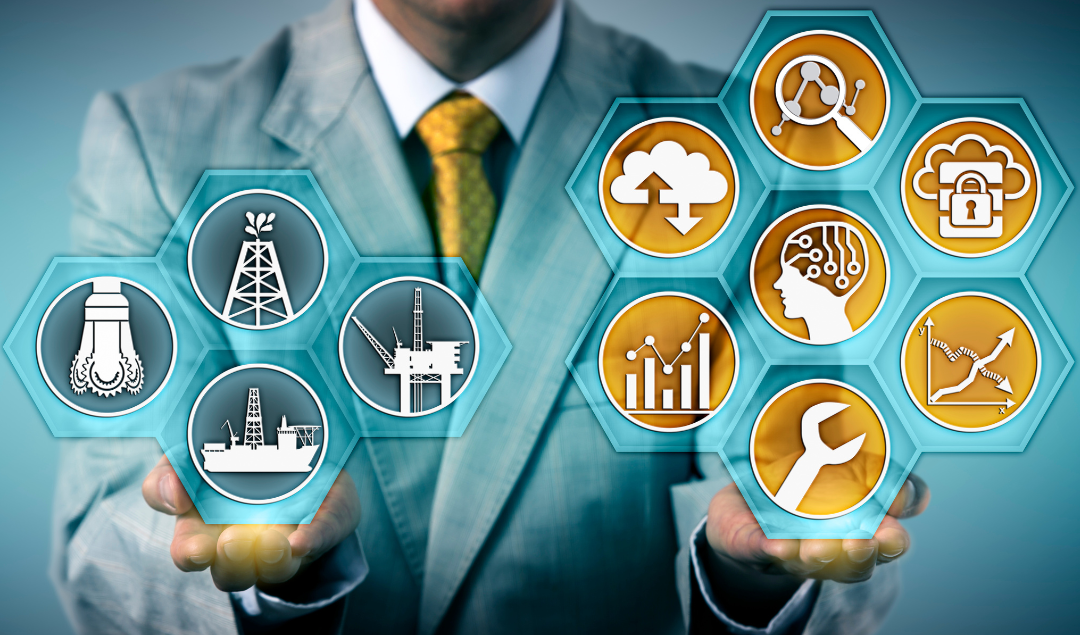
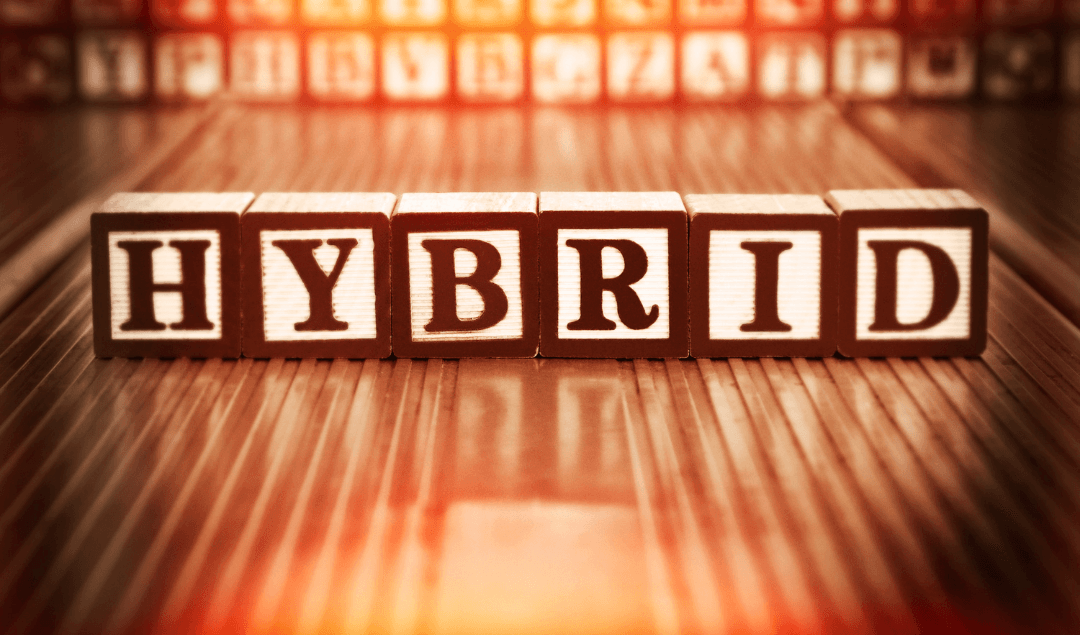
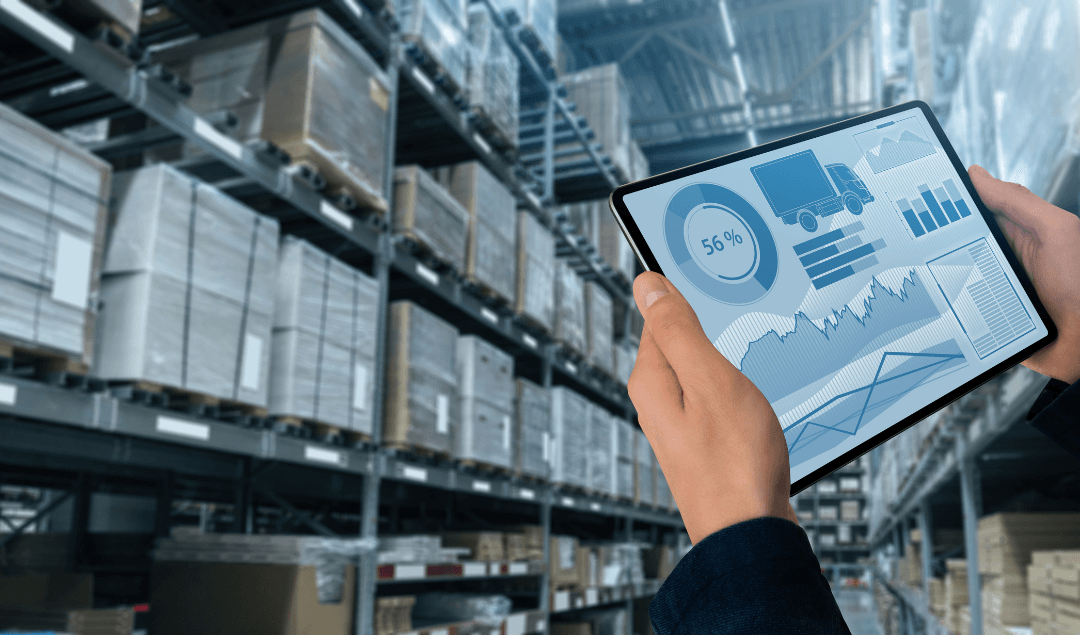