Expert Guidance and Insights in Production and Warehouse Management Systems (WMS).
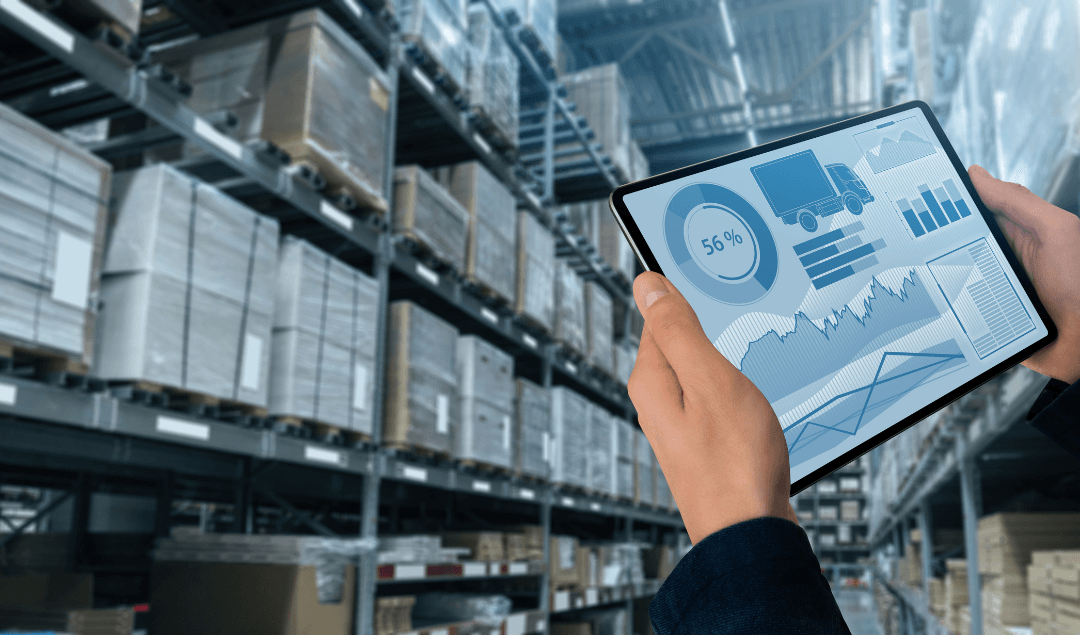
Warehouse management is essential to running a warehouse and getting items to customers on time. If you aren’t managing your warehouse with the best practices, then you risk falling behind the competition.
You are a company that sells goods. Whether you have a physical store or an online presence, the items you sell must be kept safe. This location could be a warehouse, distribution centre, or fulfilment centre. Even if you lease or rent a warehouse or outsource the logistics, proper warehouse management is critical to keeping customers satisfied.
It makes no difference whether a warehouse is stocked with the most cutting-edge technology. The best warehouses are those that run efficiently and have motivated employees, as well as low operating and logistics costs and a higher profit margin. How do you get that? To begin, you must learn about warehouse management, including what it entails and some of the best practices. Let's get started. Did you know that businesses spend more than $350 billion on warehousing each year? When your warehouse is not properly managed, the cost of having one skyrockets. However, by investing in improving the warehouse and managing it more effectively, you can reduce overall costs by up to 20%.
A warehouse management system (WMS) is a set of policies and processes designed to organize the work of a warehouse or distribution centre and ensure that it operates efficiently and meets its goals. The term 'warehouse management information system' was frequently used in the twentieth century to distinguish software that performs this function from theoretical systems. Smaller facilities may use spreadsheets or physical media such as pen and paper to document their processes and activities, which can also be considered a WMS.
However, in modern usage, the term almost always refers to computer systems. A warehouse management system's primary function is to track inventory arrivals and departures. From there, features such as recording the precise location of stock within the warehouse, optimizing the use of available space, and coordinating tasks for maximum efficiency are added.
Gartner defines WMS as follows: A warehouse management system (WMS) is a software application that helps manage and intelligently execute the operations of a warehouse, distribution, or fulfilment centre. WMS applications offer capabilities such as receiving, put-away, stock locating, inventory management, cycle counting, task interleaving, wave planning, order allocation, order picking, replenishment, packing, shipping, labour management, yard management and automated materials handling equipment interfaces.
A warehouse management system (WMS) is intended to identify existing operational processes and develop them to maximize efficiencies. The system makes it easier to manage, plan, organize, and staff warehouse materials and resources. Each warehouse management system operates according to the needs of the warehouse and provides tools and information for warehouse management. Every warehouse, in general, performs four basic functions: receiving a product, storing it, picking it, and shipping it.
Implementing a warehouse management system allows a business to gain a competitive advantage by lowering labour costs and improving inventory record accuracy. It also allows for real-time inventory management, providing timely information on orders, shipments, and receipts. Maximizing warehouse capacity can drive efficiencies that support inventory organization to increase pick, pack, and dispatch processes, thereby increasing profitability and customer satisfaction through improved service levels.
Levels of Complexity:
More complex warehouse management systems typically include specialized features designed for specific industries or facility types, whereas legacy enterprise software vendors strive to offer as many of these features as possible in a 'one-size-fits-all' solution, which may be available as modules.
Academic research has made use of an approximate classification system based on 3 levels of complexity:
1. Inventory management and location control are supported by a basic WMS. At this level, the performance data that can be produced is generally limited to 'throughput,' or how much stock moves through the warehouse in a given period of time. A basic WMS is nearly identical to a basic Inventory Management System.
2. A sophisticated WMS can analyse capacity and stock levels, as well as track how much time and labour is spent on various activities. This enables it to generate data on efficiency and suggest ways to improve it. Most WMS’s in use today outside of East Asia fall into this category. At this level, the WMS's responsibilities may begin to overlap or replace those of a Warehouse Control System or Warehouse Execution System.
3. When planning activities, a controlled WMS can exchange data with other systems to take information from outside the warehouse (e.g., manufacturing needs, customer orders, transportation) into account, and vice versa. In facilities that have automation or IoT devices, it may control or receive feedback from them. It may also use machine learning to continuously simulate or test strategies for improving operations. The most complex WMS’s are nearly identical to the most complex WES’s.
WMS software has traditionally been sold under a perpetual licence, which grants organizations the permanent right to install it on their own on-premise servers, typically in conjunction with a fixed period of updates and technical support that can be renewed at an additional cost. This provision model, like many other types of enterprise software, is gradually being replaced by hosted subscription services. Legacy enterprise software vendors typically provide both models but encourage customers to migrate to the cloud.
A warehouse management system (WMS) can be a stand-alone product or a module or group of modules within a larger Enterprise Resource Planning (ERP) or Supply Chain Management System (SCMS). The type of installation has no bearing on the level of functionality that a WMS can achieve, if sufficient computing power is available, and data is successfully synchronized with other systems.
Primary MWS Processes:
The way you manage a warehouse is frequently determined by what you are selling. Food and beverage delivery, for example, will prioritize appropriate storage within the facility and during transportation to reduce damage and spoilage. Larger home goods or clothing retailers, on the other hand, will emphasize shipping and handling. Regardless of the goals, every warehouse follows the same procedures.
1. Inventory Tracking.
Warehouse management entails keeping track of the quantity of goods on hand. Managers can use barcode scanners to determine which stock-keeping units (SKU) are available. They can also track inventory by SKU to determine storage location and order status.
2. Item Receiving and Storing.
Using a warehouse management system (WMS) is one of the best ways to simplify receiving and storing goods. Employees can use the software to quickly scan SKU barcodes and update the WMS in real time. The automated reports can then be accessed by anyone who is connected to the system from anywhere. After that, the inventory can be moved into either short- or long-term storage. When something is stored, it is scanned again, creating a record of its location.
3. Pick and Pack.
In warehouses, a pick list is used to retrieve specific quantities of an item. The list will contain information on the location, name, and SKU of each item that the employee needs to find for the packers. Once the item is located, it is delivered to the packer, who places each item in the appropriate shipping box.
4. Shipping.
Businesses can choose from a variety of shipping carriers, including DHL, UPS, the US Postal Service, and FedEx. These carriers will collect goods from a distribution centre or warehouse and deliver them. The WMS updates the customer and facility once the packaged items leave the warehouse.
5. Reporting.
Warehouse managers use software tools such as a WMS to get a real-time view of stock levels, order fulfilment, and the number of on-time shipments. Reports can also be distributed throughout the organization to assist with finances, human resources, and accurate inventory forecasting through the enterprise resource planning (ERP) system.
Best practises in Warehouse Management:
So, you want to get rid of all the guesswork and redundant tasks in the warehouse. Using a warehouse management system (WMS) and integrating it into an enterprise resource planning (ERP) system is the best thing you can do for your warehouse. Not only does this eliminate any repetitive data entry tasks, but it can also automate other critical processes and practices, such as the ones described below. Once you have a functional ERP solution, you can begin optimizing and increasing the productivity of your warehouse. Then, concentrate on these warehouse management best practices.
1. Data Collection.
Data collection and management are critical components of a well-functioning warehouse. By implementing the appropriate technologies, you can automate many warehouse processes while also reducing the number of human-made errors. This is extremely beneficial to you. You will see more accurate stock and financial representations. RFID systems and barcodes can also be used to eliminate the time-consuming logging of product movement throughout the warehouse. Aligning product identification with tracking processes will increase transparency and allow for unrestricted movement.
2. Cross-Docking.
Cross-docking is an option if you have a larger distribution centre or frequently use LTL shipments. Cross-docking cuts shipping and handling time and allows products to be transferred from one vehicle to the next. Although it requires a significant initial investment, cross-docking is a wise move for larger enterprises that need to keep stock as fluid as possible.
3. Recording Stock Movement.
If you want to effectively manage a warehouse, every step should be recorded and monitored. Some steps may be unnecessary and can be changed to better suit the warehouse's flow. Otherwise, you will be taking steps that are unnecessary and may reduce turnaround time.
4. Dynamic Slotting.
Instead of a batch process, consider slotting the warehouse based on item demand. Batches are matched with transit and shipping schedules using dynamic slotting, giving you more flexibility during the pick-and-pack process.
5. Health and Safety.
One of the most important things you can do for a warehouse is to prioritize employee health and safety. Ensure that goods are secure, protocols are followed, and productivity remains high. This is possible with a WMS, which eliminates redundant steps. Continuously evaluate the warehouse layout to improve accessibility and reduce work-related incidents or damaged goods.
6. Advanced Shipping Notifications.
Regular shipping and receiving are bound to encounter schedule disruptions and delays. This reduces warehouse efficiency and may strain relationships with customers, distributors, suppliers, and carriers. You can correct some issues caused by supply chain disruptions by implementing electronic shipping notifications. You can also cut down on labour shortages and wasted time.
Optimize your Warehouse Management today. Warehouse management is essential to running a warehouse and getting items to customers on time. If you aren’t managing your warehouse with the best practices, then you risk falling behind the competition. Get the most out of your warehouse by partnering with MWare. Our intuitive Connector integrates with any ERP system, so you can leverage your warehouse with more ease and stability.
Improve your production and warehouse management challenges with MWare Consulting.
We offer advanced production and MWS solution capabilities that support operations best practices which you need to manage your business more efficiently. To learn more schedule a demo today.
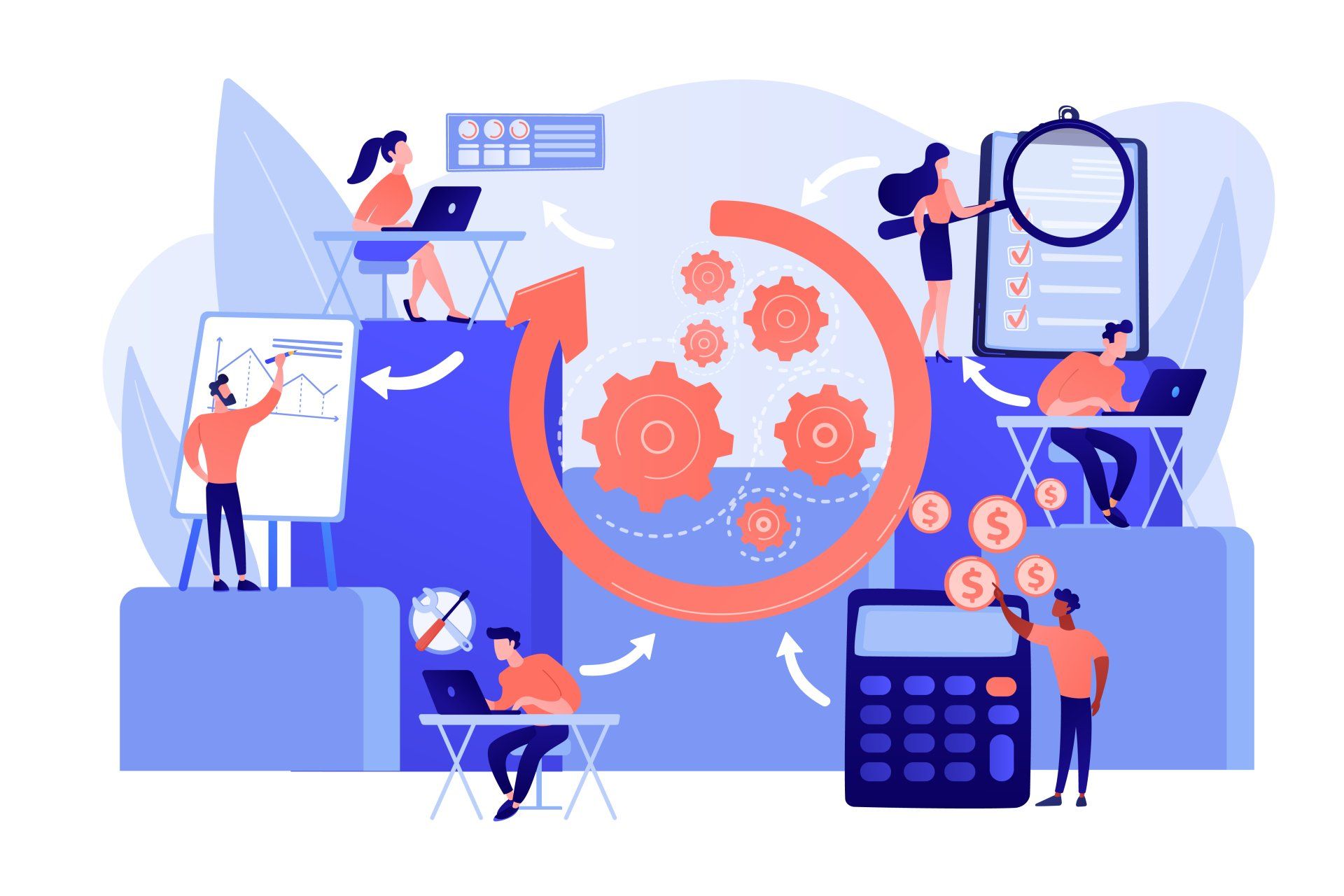
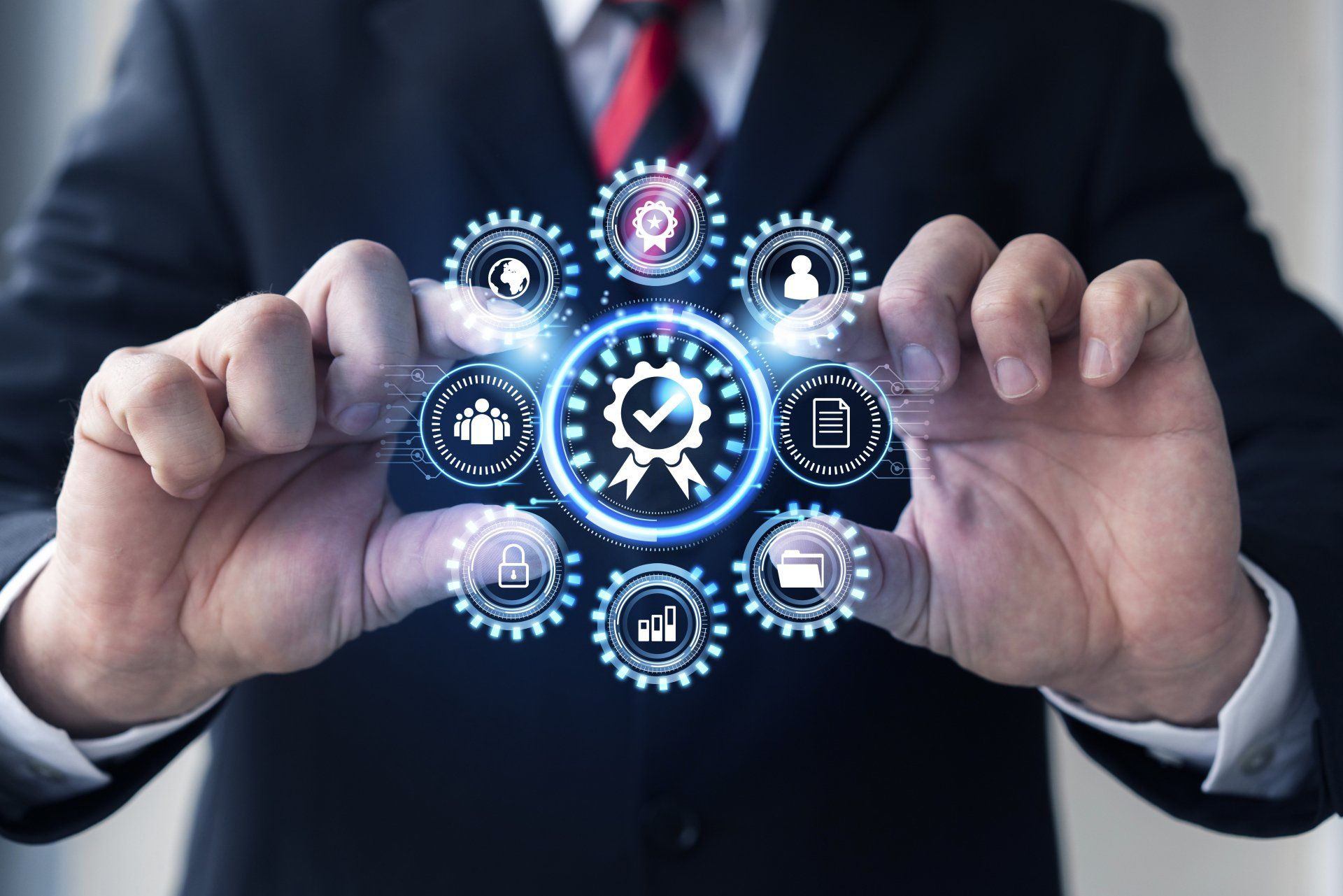
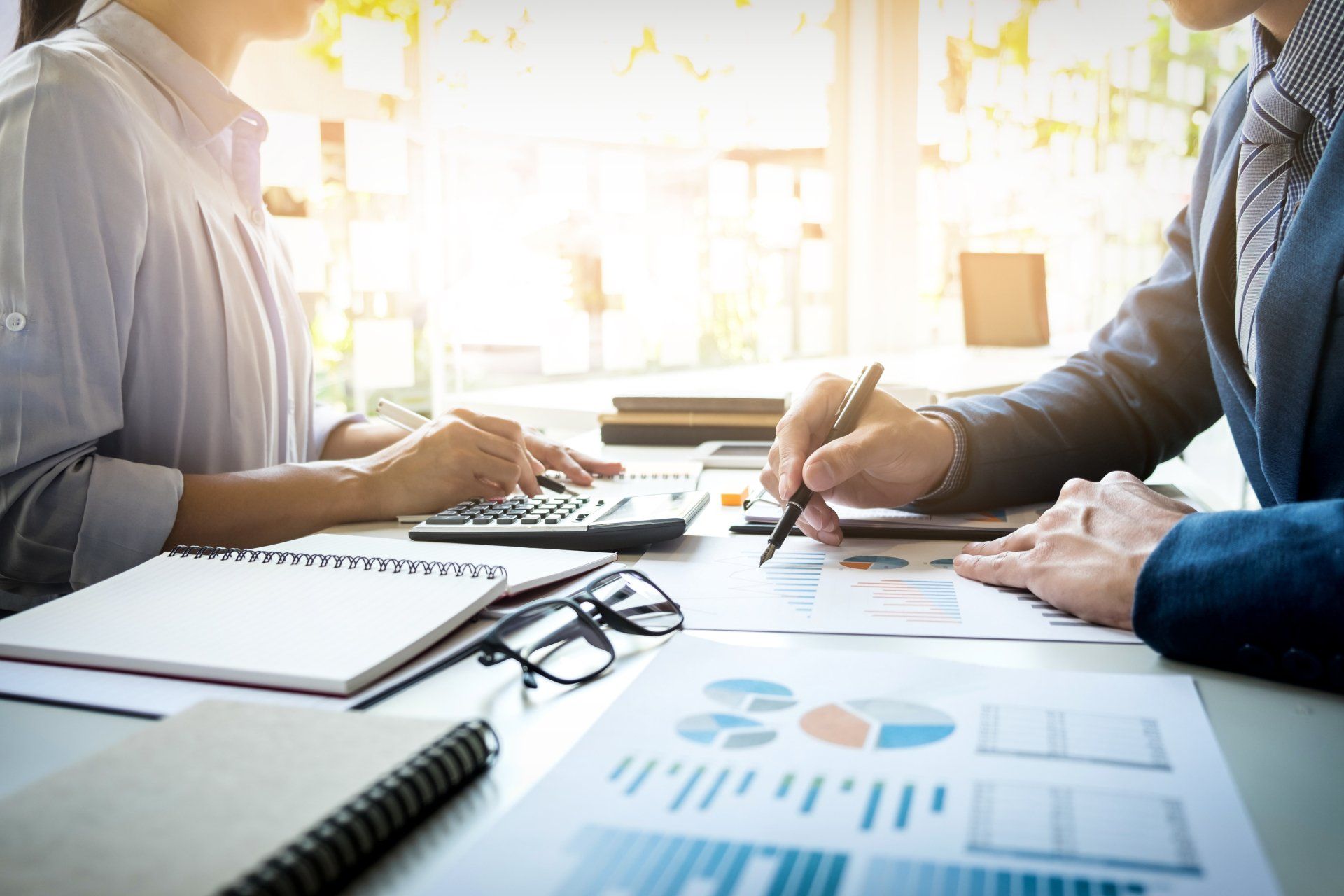
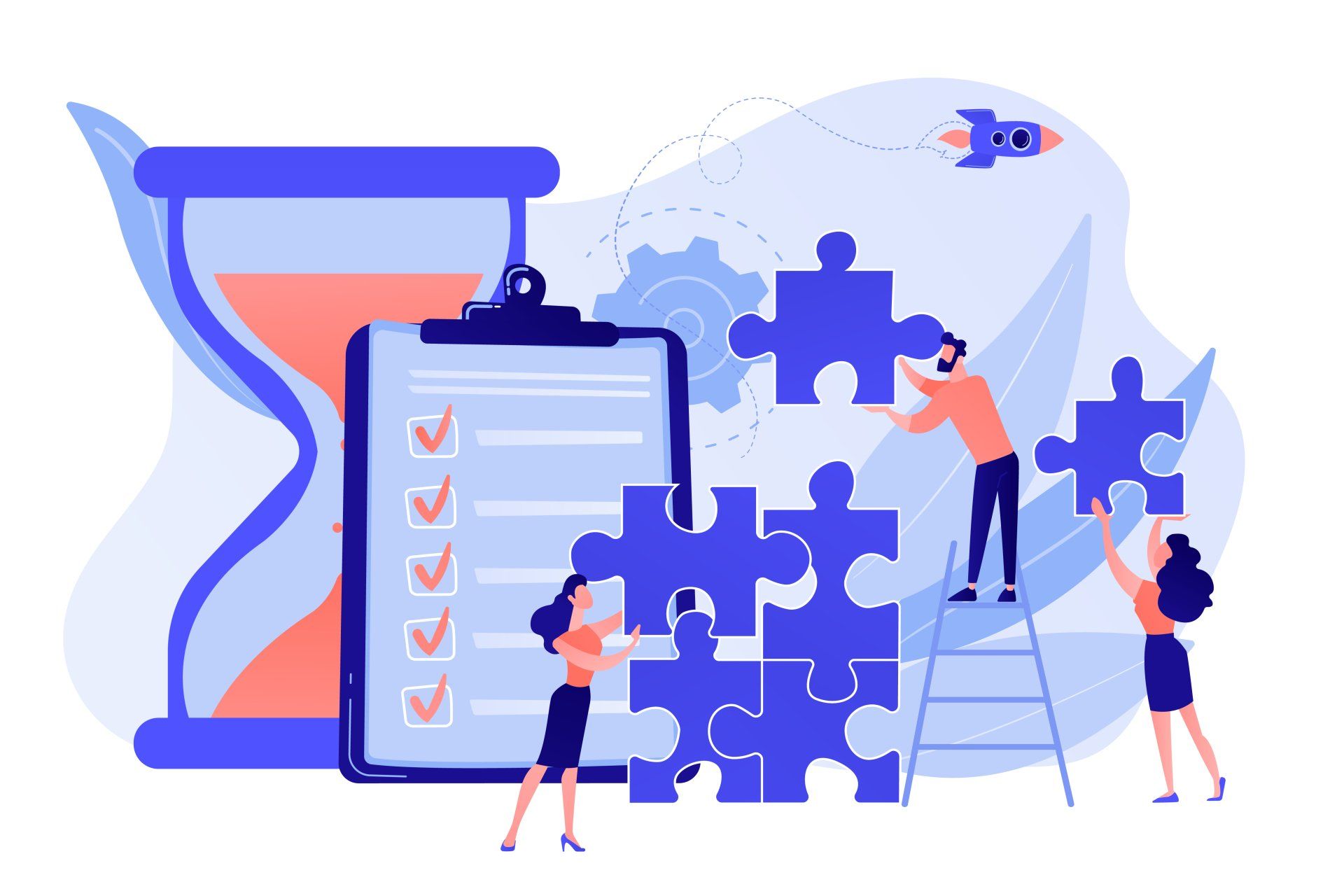
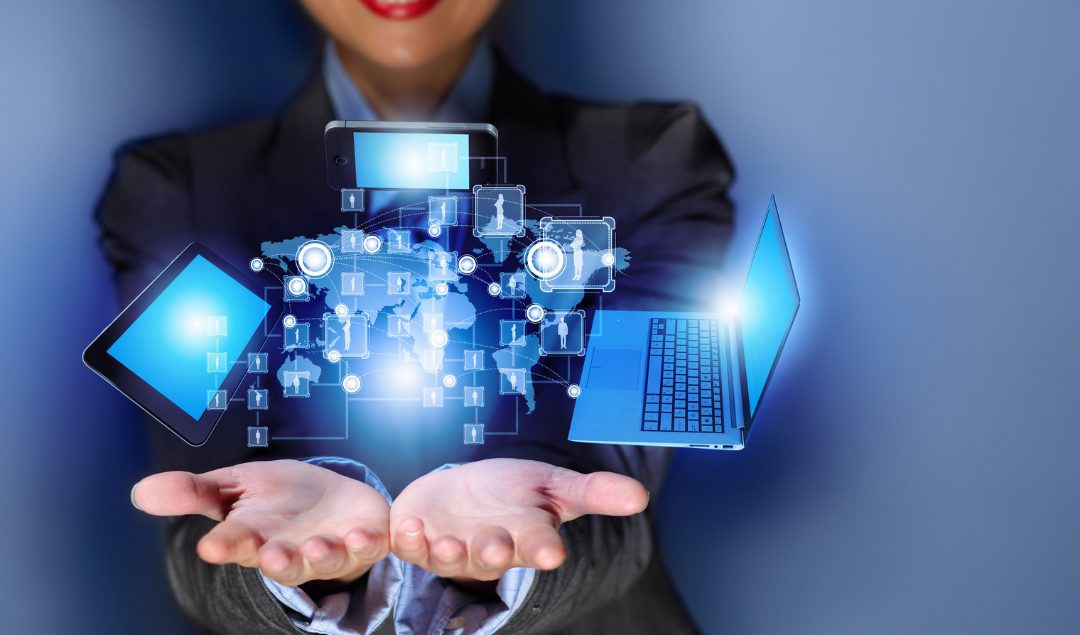
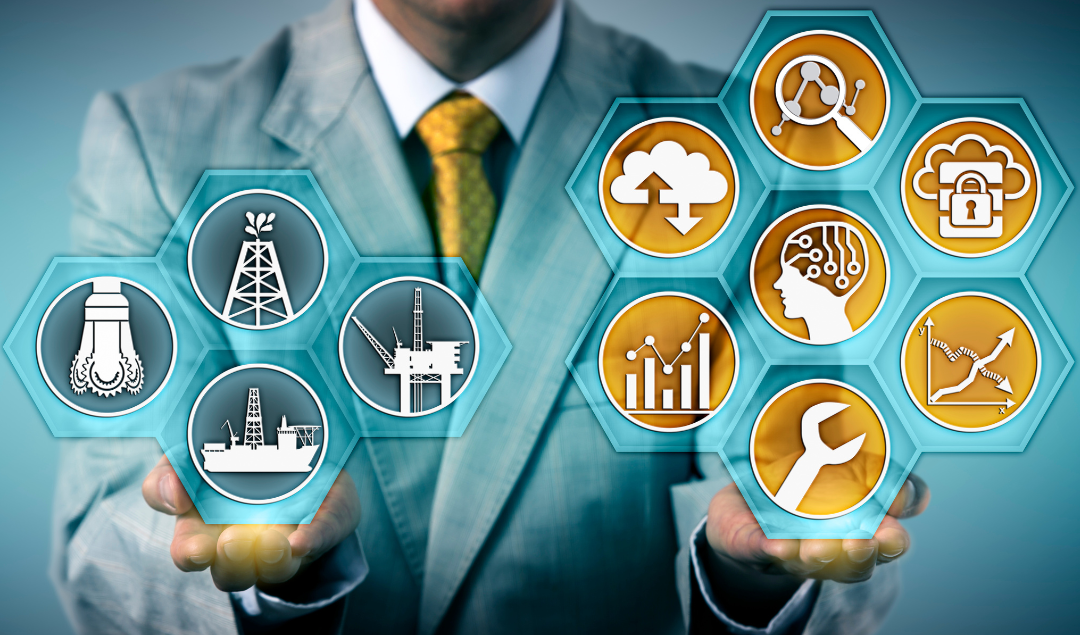
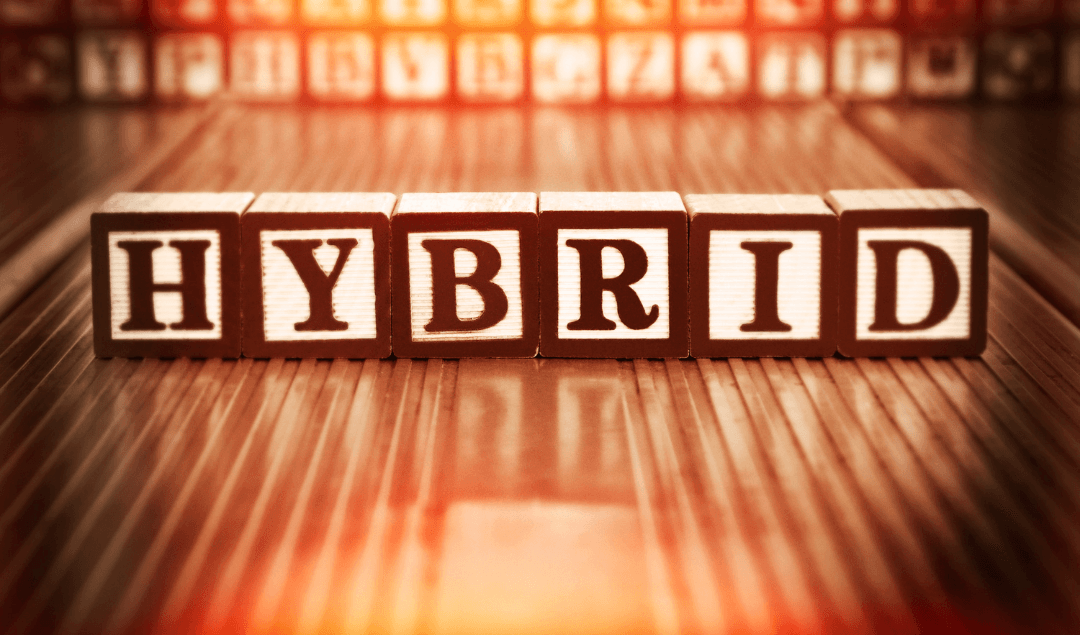